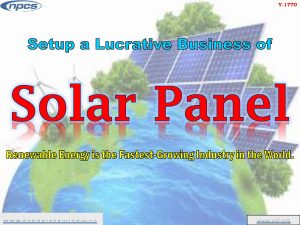
A solar panel is made up of a number of solar cells. A vast number of little solar cells spread out over a vast area can combine to provide enough electricity to be useful. The more light a cell receives, the more electricity it generates. As a result, spacecraft are typically designed with solar panels that can always be pointed at the Sun as the rest of the spaceship moves around, similar to how a tank turret can be targeted regardless of where the tank is heading. PV panels, commonly known as solar panels, absorb and convert the sun's energy into electricity. PV panels generate electricity that is mostly utilized to power household appliances and equipment. The most common PV panel system is the grid-connected system, which is connected to the national grid as its name implies.
Related Project:- Solar Panel- Manufacturing Plant, Detailed Project Report, Profile, Business Plan, Industry Trends, Market Research, Survey, Manufacturing Process, Machinery, Raw Materials, Feasibility Study, Investment Opportunities, Cost And Revenue, Plant Economics
This means it can draw electricity from the grid at night when the solar panels aren't working. PV panels come in a variety of shapes and sizes, and they may easily be installed on top of an existing roof. Solar roof tiles are an alternative to solar panels that take up less rooftop space but are more expensive. A photovoltaic system's solar panel, also known as a solar module, is one of its components. They are made up of a panel made up of a succession of solar cells. They come in a variety of rectangular designs and are used to generate power in groups. Solar panels, also known as photovoltaic panels, absorb energy from the Sun in the form of sunlight and convert it to electricity that can be used to power homes or businesses. These panels can be used to complement a building's electrical supply or to deliver power to remote areas.
Uses of Solar Panel:
Solar panels are a cost-effective technique to generate electricity for a variety of uses. Off-grid living is the most apparent choice. Living off-grid entails residing in a location that is not connected to the main power grid. Solar power systems are ideal for remote homes and cabins. It is no longer required to pay exorbitant rates to have electric utility poles and cabling installed from the nearest main grid access point. A solar electric system is theoretically less expensive and, if properly maintained, can produce power for up to three decades.
Books: - BOOKS & DATABASES
A part from the fact that solar panels allow people to live off the grid, probably the most significant advantage of solar power is that it is a clean and renewable source of energy. With the onset of global climate change, it is more necessary than ever to do everything we can to lessen the strain on our atmosphere caused by greenhouse gas emissions. To help support the panel structure, solar panels also include metal frames that include racking components, brackets, reflector shapes, and troughs. Concentrators, which focus light through lenses or mirrors onto smaller cells, are one type of special solar PV module. This enables the cost-effective usage of cells with a high cost per unit area (such as gallium arsenide).
Manufacturing Process:
1. Cell Cutting: Cells are carved out using a laser cutting machine. The size of a cell is governed by the wattage that the panels require. This step is avoided for modules with a full cell size.
2. Stringing Procedure: The stringing process is totally automated. The upper (Blue/Black) Sun-facing side is negative, whereas the lower (White) side is positive.
3. Solar Glass: After the cells are strung together, the machine transfers them to tempered glass with an ethylene vinyl acetate (EVA) encapsulation layer.
4. Visual Inspection: A technician examines the cells for any faults or errors in the strings.
5. Taping: A technician tapes the cells into a matrix alignment during taping.
6. Soldering: After that, the connections are soldered together. Any extra material is removed.
7. Insulate Module Connections: The next step is to use a back sheet and EVA encapsulation to insulate the connections. This procedure safeguards the module against dust and moisture.
8. Mirror Inspection: The module is visually inspected once more for dust particles, color mismatches, and other issues.
9. EI Testing: EI Testing, also known as Electroluminescence Testing, is the actual testing of the module. It's a kind of scanning technique in which the module is scanned in an EI machine.
Related Videos: Renewable Energy Sector, Green Power, Solar Energy, Biofuel, Hydroelectric, Wind, Non-conventional Energy, New and Renewable Energy
10. Lamination: The module is laminated at a temperature of 140 degrees Celsius. This procedure takes about 20 minutes. After lamination, the modules are allowed to cool for 10-15 minutes until they reach room temperature.
11. Trimming the Back Sheet: To manufacture correctly shaped modules, this step entails cutting off the surplus material from the back sheet.
12. Frame Cutting: Frames of various widths are carved out for bordering the panels in this stage.
13. Punching Holes in the Frames: Holes are punched in the frames for mounting and grounding the panels.
14. Filling/Framing with Sealant: A sealant protects the panels from air, dust, and moisture while also assisting the module's secure attachment to the frame. After the frame has been mounted to the module, it is sent back to the framing machine to be punched to ensure that it is permanently attached to the frame.
15. Attaching the Junction Box: A junction box is fastened to the module using sealant to keep it firmly in place. The connections are then soldered and let to cure for 10-12 hours, ensuring that the structures are completely dry and correctly bonded.
16. Wipe Outside the Module: The module is wiped outside to remove any dust, foreign particles, or excess sealant.
17. Module Testing: The module is attached in order to examine the output current, voltage, and power, among other things. For each module's output data, a report is generated. For the benefit of the users, a black label (with full details) is pasted behind the module.
18. Packing: This is the last phase in the module production process, after Final Quality Assurance (FQA), when the modules are safely packed into huge boxes for shipping and storage.
Market Outlook:
The global market for solar PV panels was estimated at USD 115.2 billion in 2019, with a compound annual growth rate (CAGR) of 4.3 percent expected from 2020 to 2027. Increased environmental degradation and government incentives and tax refunds to install solar panels are driving the growth of the solar energy business. Furthermore, the reduced water footprint of solar energy systems has boosted their demand in the power generation sector. The market for solar cells has grown significantly as a result of an increase in rooftop installations, followed by an increase in architectural applications.
Profile- Project Reports & Profiles
The solar panel market will be driven by rising electricity prices combined with lower-cost solar panels. Rising demand for solar panels in the residential rooftop solar industry, as well as cheap prices for polysilicon and silver used in solar cell manufacture, will help the market accelerate in the coming years. Furthermore, the falling cost of solar panels has prompted governments in a number of countries to take more initiatives and provide subsidies, which is projected to aid the growth of the residential solar panel market.
Renewable Energy Industry in India:
In the early 1980s, India became the first country in the world to establish a ministry of non-conventional energy resources (Ministry of New and Renewable Energy (MNRE)), and the Solar Energy Corporation of India, one of its public sector organizations, is responsible for the development of the solar energy industry in India. India is one of the countries that produces a significant amount of renewable energy. As of November 27, 2020, renewable energy sources account for 38% of India's installed electricity producing capacity (136 GW out of 373 GW). India's renewable energy business is the world's fourth most appealing renewable energy market.
Market Research: - Market Research Report
India came in fifth place in wind power, fifth place in solar power, and fourth place in renewable energy. This is the world's greatest renewable energy expansion strategy. Renewable power generation capacity has grown at a rapid pace in recent years, with a CAGR of 17.33% from FY16 to FY20. The sector has grown more appealing to investors as a result of increasing government assistance and improved economics. The country has set a lofty goal of achieving 175 GW of renewable energy capacity by the end of 2022, with the goal of increasing to 450 GW by 2030. Renewable energy will play an essential part as India attempts to fulfill its own energy demand, which is anticipated to reach 15,820 TWh by 2040.
Key Players:
1. A M P L Cleantech Pvt. Ltd.
2. Aatash Power Pvt. Ltd.
3. Brightsolar Renewable Energy Pvt. Ltd.
4. Cial Infrastructures Ltd.
5. Cleansolar Renewable Energy Pvt. Ltd.
6. Dhursar Solar Power Pvt. Ltd.
7. Divine Solren Pvt. Ltd.
8. Ind Renewable Energy Ltd.
9. Indira Power Pvt. Ltd.
For More Detail: https://www.entrepreneurindia.co/project-and-profile-listing?CatId=82&SubCatId=82&CatName=Renewable%20Energy
#DetailedProjectReport #businessconsultant #BusinessPlan #feasibilityReport #NPCS #entrepreneurindia #startupbusiness #ProjectReport #startup #projectconsultancy #businessopportunity #SolarPanel #SolarPanelMarket #SolarEnergy #SolarPanelIndustry #SolarCellManufacturing #SolarSector #SolarMarket #RenewableEnergy #solarEnergyBusiness #photovoltaicsystems