Jute shopping Bags
INTRODUCTION
Bags prepared from jute are widely used in our country for domestic purposes. It is used largely in our country before 10-15 years, during the year 1985-1995. Plastic bags are taken large share over it. Plastic bags have certain advantage over the jute bags, i,e, they are light, appearance good, easily decorative, moisture protective, self life higher, above all the merits there is all over the world, i,e, plastics are non-biodegradable which makes environmental pollution, it cannot be used for land filling material. For the above reasons, european country's about to take decision to band, the use of nondegradeable plastic in general domestic purpose. They are highly interest to use such materials which are easily bio-degradeable and non-carcinogenic. Jute is one of the agricultural product which can fill up the partial gap of the plastic items. Now in world India is one of the country's where jute using hybrid technology or tissue culture process to increase the jute production yield per unit land area. By which India can export different jute items by fulfilling domestic demands and earn more foreign exchange.
Jute shopping bag is a item which has large demand in our domestric market as well as in the export market.
USES
It is used for bringing daily usable goods from groeer shop, vegetable from market and necessary small utensils etc.
PROPERTIES
It has high surface friction (allowing stacking of filled bags to a high level) porus structure and moisture absorbing capacity. High tearing strength resistance to damage cause by hooking and self closing of hole made by hooking, suitable to reuse, and easy to disposability without causing pollution to environment. Bags weight are around 300 gm - 700 gms.
MANUFACTURING PROCESS
Fabrics prepared form low grade or medium grade jute fibre (sacking) are used for the manufacturing of jute bags usually used for domestic purpose in our country and fabrics prepared from of white jute yarn (Hessian) are generally used for export purpose.
Fabrics are taken and pass over through sizing table to cut the fabrics in proper size according to requirement. (Size may be varied from height 15" - 30" and width 10" - 25" generally without handle). After proper sizing of fabrics are pass over to the sewing machine to make bag or fabrics may pass thorough the automatic bag making machine to form bag by controlling switch according to requirement. When the stitching of bags are over then put the handles on the bag and make the stiffening border over the bag to make it proper strength.
For making decorative bags use decorative fabrics.
PROCESSING FLOW SHEET
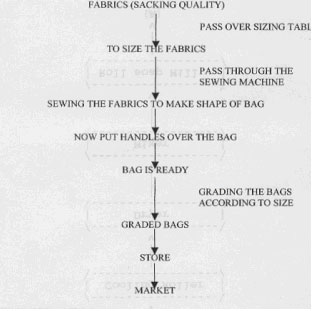
NAME OF THE MANUFACTURE
1. Hindustan Knitting and Finishing Mills,
16A, Najafgarh Road,
New Delhi - 15.
2. Sri Saravana Veal Mills,
39, Kuma Nagar East.,
Tirpur - 638 603, India
3. Capital Hosiery Industry
1449, Pan Mandi,
Sadar Bazar,
Delhi - 110 006.
4. Asoke Hosiery Works,
A-131, Industrial Area,
Wazirpur,
Delhi - 110 052.
NAME OF THE MACHINERY SUPLIERS
1. Ambia Texmech Manufactures (P) Ltd.,
B-13, NOble Chamber (VATSA HOUSE),
Gogha Street, Fort,
Bombay - 400 001.
2. Textool Company Ltd.,
Ganapathi,
Coimbatore - 641 006
3. Texcomast Export.
2, Arcadia,
Nariman Point,
Bombay - 400 021.
4. Bimag Machines Pvt. Ltd.,
309, Dalmal Towers,
Nariman Point,
Bombay - 400 021.
5. Perna Textie Industries Pvt Ltd.,
212/213, T.V. Industrial Estate,
(2nd floor) Plot No. 248A, 52,
S.K. Ahire Marg, Worli,
Bombay - 400 025.
PLANT ECONOMICS
=
Rated Plant capacity Basis |
= |
1000.00 No. per day |
No. of working days |
= |
25 days per month |
|
300 days per annum |
No. of shifts |
= |
1 per day |
One shift |
= |
8 hours |
LENGTH 76 CM.
WIDTH 50 CM.
LAND & BUILDING
1. |
Land required 200 sqm. (@Rs. 500/- per sqm.) |
Rs. |
1,00,000.00 |
2. |
Built up area 100 sqm. (@Rs. 1500/- sqm.) |
Rs. |
1,50,000.00 |
3. |
Land development cost |
Rs. |
25,000.00 |
|
TOTAL |
Rs. |
2,75,000.00
|