Acrylic Acid and Derivatives
The term acrylates includes derivatives of both acrylic (CH2==CHCO2H) and met acrylic acid (CH2==CH (CH3) CO2H). This article discusses the preparation, properties, and reactions of acrylic acid monomers only.
Acrylic acid (propenoic acid) was first prepared in 1847 by air oxidation of acrolein (1). Interestingly, after use of several other routes over the past half-century, it is this route, using acrolein from the recently developed catalytic oxidation of propylene, that is currently the most favoured industrial process. Polymerization of acrylic esters has been known for just over a century. However, it was only about 1930 that the technical difficulties of their manufacture and polymerization were overcome. The rate of consumption of acrylates has been growing between 10 and 20% annually and continued good growth, perhaps at the 10% rate, is expected for at least the next decade. It is also expected that manufacture will continue to be concentrated in the United States, Europe, and Japan. United States manufacturing capacity for acrylic acid and esters is about 500 kilotons per year and represents about half of world capacity.
Acrylates are primarily used to prepare emulsion and polymers. The emulsion polymerization provides high yields of polymers in a form suitable for a variety of applications. Acrylate polymer emulsions were first used as coatings for leather in the early 1930s and have found wide utility as coatings, finishes, and binders for leather, textiles, and paper. Acrylate emulsions are used in the preparation of both interior and exterior paints, floor polishes, and adhesives. Solution polymers of acrylates, frequently with minor levels of other monomers, are employed in the preparation of industrial coatings.
The polymeric products can be made to vary widely in properties through controlled variation in the ratios of monomers employed in their preparation, cross linking, and control of molecular weight. They share common qualities of high resistance to chemical and environmental attack, excellent clarity, and attractive strength properties. In addition to acrylic acid itself, methyl, ethyl, butyl, and 2- ethylhexyl acrylates are manufactured on a large scale and are available in better than 98-99% purity. They usually contain 10-200 ppm of hydroquinone monomethyl ether as polymerization inhibitor. Other grades containing hydroquinone are also available.
Physical Properties
Table 1 lists several physical properties of acrylic acid and representative derivatives. Table 2 gives properties for commercially important acrylic esters, whereas Table 3 lists the physical properties of other esters.
Acrylic acid is a moderately strong carboxylic acid. Its dissociation constant is 5.5x10-5. Vapor pressure as a function of temperature is given in Table 4 for acrylic acid and four important esters. The lower esters form azeotropes both with water and with their corresponding alcohols.
Reactions
Acrylic acid and its esters may be viewed as derivatives of ethylene in which one of the hydrogen atoms has been replaced by a carboxyl or carboalkoxyl group. This functional group may display electron-withdrawing ability through inductive effects of the electron-deficient carbonyl carbon atom, and electron-releasing effects by resonance involving the electrons of the carbon-oxygen double bond. Therefore, these compounds react readily with electrophilic, free radical, and nucleophilic agents.
Functional Group Reactions. Polymerization is avoided by conducting the desired reaction under mild conditions and in the presence of polymerization inhibitors.
Acrylic acid undergoes the reactions of carboxylic acids and can be easily converted to the following derivatives.
- Salts, by reaction with an appropriate base in aqueous medium. They can serve as monomers and commoners in water- soluble or water-dispersible polymers for floor polishes and flocculants.
- Acrylic anhydride, by treatment with acetic anhydride or by reaction of acrylate salts with acryloyl chloride.
- Acryloyl chloride, by reaction with phosphorous oxychloride, or benzoyl or thionyl chloride. Neither the anhydride nor the acid chloride is of commercial interest.
- Esters, by a variety of routes below, are of major interest because most acrylic acid is the form of its methyl, ethyl, and butyl esters. Specialty monomeric esters with a hydroxyl, amino, or other functional group are used to provide adhesion, latent crosslinking capability, or different solubility characteristics.
- Direct esterification with alcohols in the presence of a strong acid catalyst such as sulfuric acid, a soluble sulfonic acid or sulfonic acid resins.
- Addition to alkylene oxides gives hydroxyalkyl acrylic esters.
- (c) Acrylic acid adds to the double bond of olefins in the presence of strong anhydrous acid catalyst.CH2==CHCO2H+CH2==CH2 H+ CH2==CHCO2CH2CH3
- Amides, by reaction with ammonia or primary or secondary amines. However, acrylamide is better prepared by controlled hydrolysis of acrylonitrile. Acrylates can also be obtained by carrying out the nitrile hydrolysis in the presence of alcohol.Acrylic esters may be saponified, converted to other esters (particularly of higher alcohols by acid catalyzed alcohol interchange), or converted to amides by aminolysis, Transesterification is complicated by the azeotropic behavior of lower acrylates and alcohols, but is useful in preparation of higher alkyl acrylates.
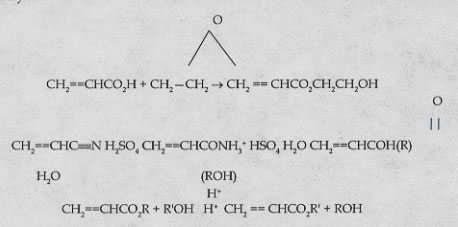
Unsaturated Group Reactions
Free radical-initiated polymerization of the double bond is the most common reaction and presents one of the more troublesome aspects of monomer manufacture and purification. Substituted ring compounds are formed readily by Diels-Alder reactions.
CH2==CHCO2R + CH2 == CH-CH==CH2 ® CO2R
Additions. Halogens, hydrogen halides, and hydrogen cyanide readily add to acrylic acid to give the 2,3-dihalopropionate, 3-halopropionate, and 3-cyanopropionate, respectively.
On storage or at elevated temperatures, acrylic acid dimerizes to give 3-acryl-oxypropionic acid.
2CH2==CHCO2H CH2==CHCO2CH2CH2CO2H
Continuation of this reaction leads to a distribution of polyester oligomers formed by successive additions across the double bond. Acrylic acid can be regenerated by thermal or acid catalyzed cracking of these oligomers. Cracking of the corresponding esters gives acrylic esters.
CH2==CHCO2CH2CH2CO2R H+ CH2==CHCO2H + CH2 == CHCO2R
Michael condensations are catalyzed by alkali alkoxides, tertiary amines, and quaternary bases and salts. Active methylene compounds and aliphatic nitro compounds add to form b-substituted propionates. These addition reactions are frequently reversible at high temperatures. Exceptions are the tertiary nitro adducts which are converted to olefins at elevated temperatures.
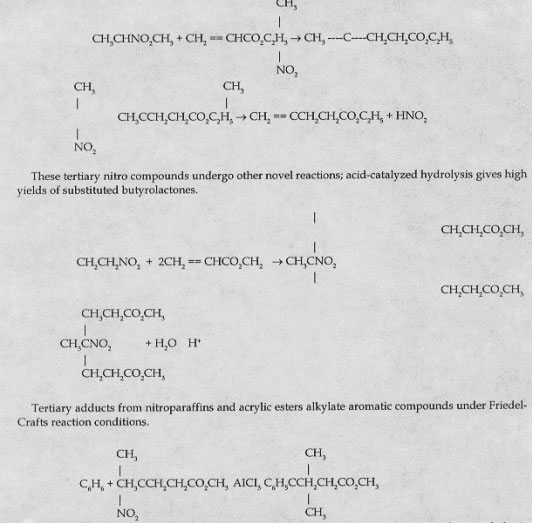
The addition of alcohols to form the 3-alkoxypropionates is readily carried out with strongly basic catalyst. If R and R' are different, ester interchange gives a mixture of products. Anionic polymerization to oligomeric acrylate esters can be obtained with appropriate control of reaction conditions.
The 3-alkoxypropionates can be cleaved in the presence of acid catalysts to generate acrylates. Recent developments in transition metal catalysts for carbonylation of olefins provide routes to both 3-alkoxypropionates and 3-acryloxypropionates. Hence, these are potential routes to acrylates from ethylene and carbon monoxide but they have not been developed commercially.
Addition of mercaptans with alkaline catalysts give 3-alkylthiopropinates. In the case of hydrogen sulfide, the initially formed 3-mercaptopropionate reacts with a second molecule of acrylate to give a 3,3'-thiodipropionate.
H2S + 2CH2==CHCO2R ® S (CH2CH2CO2R)2
Polythiodipropionic acids and their esters are prepared from acrylic acid or an acrylate with sulfur, hydrogen sulfide, and ammonium polysulfide. These polythio compounds are converted to the dithio analogs by reaction with an inorganic sulfite or cyanide. The dithio compounds are useful intermediates for preparation of isothioazolones, which have shown biocidal activity for microorganisms.
CH2==CHCO2CH3+Sx + H2S (NH4)2Sx
Sx(CH2CH2CO2CH3)2 NaCN CH3OCOCH2CH2SSCH2CH2CO2CH3
Ammonia and amines add to acrylates to form b-aminopropionates, which add easily to excess acrylate to give tertiary amines. The reactions are reversible.
H3N + CH2 == CHCO2R ® H2NCH2CH2CO2R CH2==CHCO2R
HN (CH2OH2CO2R)2 CH2==CHCO2R N (CH2CH2CO2R)3
Aqueous ammonia and acrylic esters give tertiary aminoesters which form the corresponding amide upon ammonolysis.
Acrylic esters dimerize to give the a-methylene glutaric acid esters catalyzed by tertiary organic phosphines or preferably organic phosphorous triamides, phosphonous diamides, or phosphinous amides. Yields of 75-80% dimer together with 15-20% trimer are obtained. Reaction conditions can be varied to obtain high yields of trimer, tetramer, etc.
Manufacture
Various methods for the manufacture of acrylates are summarized in Figure 1, showing their dependence on specific hydrocarbon raw materials. For a route to be commercially attractive the raw material costs and utilization must be low, plant investment and operating costs not excessive, and waste disposal charges minimal.
A lead-time of several years for development and plant construction is important in a period where costs and availability of hydrocarbon raw materials are changing rapidly and significantly. Natural gas costs are expected to increase steadily while the supply is decreasing. Acetylene should be in short supply with rising costs in the next decade unless new technology based on coal is developed. Hence, acrylate manufacture by acetylene routes will become increasingly uneconomical. Ethylene costs, dependent on crude oil, are expected to increase, but not sharply. Propylene may be considered a by-product from the large volume manufacture of ethylene from heavy petroleum feedstocks. New ethylene facilities, based on naphtha and other heavy feedstocks, will ensure a large supply of coproducts including propylene. Propylene requirements for acrylates will be small, compared to other chemical uses (polypropylene, acrylonitrile, propylene oxide, isopropanol, and cumene for acetone and phenol). Hence, although the cost of propylene is also expected to rise, this should be at a slower rate than the increases for any of the other raw materials. The favorable supply and cost projections for propylene suggest that all new acrylate plants will employ propylene oxidation technology for at least the next two decades.
The most economical process for the manufacture of acrylates is based on the two-stage vapor-phase oxidation of propylene to acrylic acid.
Propylene Oxidation. The propylene oxidation process is attractive because of the availability of highly active and selective catalysts and the relatively low cost of propylene. It proceeds in two stages giving first acrolein and then acrylic acid.
CH2==CH-CH3+O2® CH2==CHCHO + H2O
CH2==CH-CHO+ ½ O2 ® CH2==CH-CO2H
Single-reaction-step processes have been studied. However, selectivity is possible by optimizing catalyst composition and reaction conditions for each of these two-step. This more efficient utilization of raw material has led to two separate oxidation stages in all commercial facilities. A two-step continuous process without isolation of the intermediate acrolein was first described by the Toyo Soda Company. A mixture of propylene, air, and steam is converted in the first reactor mainly to acrolein. The effluent from the first reactor is then passed directly to the second reactor where the acrolein is oxidized to acrylic acid. The products are absorbed in water to give about 20% aqueous acrylic acid in about 70% yield based on propylene.
Catalysts. Catalyst performance is the most important factor in the economics of an oxidation process. It is measured by activity (conversion of reactant), selectivity (Conversion of reactant to desired product), rate of production (production of desired product per unit of reactor volume per unit of time), and catalyst life (effective time on-stream before significant loss of activity or selectivity).
Early catalysts for acrolein synthesis were based on cuprous oxide and other heavy metal oxides deposited on inert silica or alumina supports. Later, catalysts more selective for the oxidation of propylene to acrolein and acrolein to acrylic acid were prepared from bismuth, cobalt, iron, nickel, tin salts, molybdic, molybdic phosphoric, and molybdic silicic acids. Preferred second-stage catalysts generally are complex oxides containing molybdenum and vanadium. Other components, such as tungsten copper, tellurium, and arsenic oxides, have been incorporated to increase low-temperature activity and productivity.
Catalyst performance depends on composition, the method of preparation, support, and calcination conditions. Catalyst specifications include, in addition to chemical performance requirements, surface area, porosity, density, pore-size distribution, hardness, strength, and resistance to mechanical attrition.
Patents claiming specific catalysts and processes for their use in each of the two reactions have been assigned to Japan Catalytic, Sohio, Toya Soda, Rohm and Haas, Sumitomo, BASF, Degussa, Ugine Kuhlmann, Asahi Glass, Celanese and others.
Oxidation Step. The oxidation process flow sheet (Fig.2) shows equipment and typical operating. The reactors are of the fixed-bed shell-and tube type (about 3-5m long and 2.5cm in diameter) with a molten salt coolant the shell side. The tubes are packed with catalyst, a small amount of inert material at the top serving as a preheater section for the feed gases. Vaporized propylene is mixed with steam and air and fed to the first-stage reactor the feed composition is typically 4-5% propylene, 30-40% steam, and the remainder air.
The preheated gases react exothermically over the first-stage catalyst with the peak temperature in the range of 330-4300C, depending on conditions and catalyst selectivity. The conversion of propylene to waste gas (carbon dioxide and carbon monoxide) is more exothermic than its conversion to acrolein. At the end of the catalyst bed, the temperature to the mixture drops to ward that of the molten salt coolant.
The acrolein-rich gaseous mixture containing some acrylic acid. Here. The temperature peaks in the range of 280-3600C, again depending on conditions. The temperature of the effluent from the second-stage reactor again approximates that of the salt coolant. The heat of reaction is recovered as steam in external waste-heat boilers.
The process is operated at the lowest temperature consistent with high conversion increases with temperature; the selectivity generally decreases only with large increases in temperature. Catalyst life also decreases with increasing temperatures. Catalysts are designed to give high performance over a range of operating conditions permitting gradual increase of salt temperature over the operating life of the catalysts to maintain productivity activity.
The gaseous reactor effluent (from the second-stage oxidation) is fed to the bottom of the aqueous absorber and cooled from about 250 to less than 800C by contact with aqueous acrylic acid. The gas passes through the absorber to complete the recovery of product. The water is fed to the top of the absorber at about 30-600C to minimize acrylic acid losses and the absorber off-gas is sent to a flare or to a furnace to convert all residual organic material to waste gas. The aqueous effluent form the bottom of the absorber is 20-30% acrylic acid which is sent to the separations section for recovery. The overall yield of acrylic acid in the oxidation reaction steps is in the range of 73-83% depending on the catalyst and conditions employed.
Acrylic Acid Recovery. The process flow sheet (Fig. 3) shows equipment and conditions for the separation step. The acrylic acid is extracted from the absorber effluent with solvent, such as butyl acetate, xylene, diisobutyl ketone, or mixtures, chosen for high selectivity for acrylic acid and low solubility for water and by-products. The extraction is performed using 5-10 theoretical stages in a tower or centrifugal extractor.
The extract is vacuum distilled in the solvent-recovery column which is operated at low bottom-temperatures to minimize the formation of polymer and dimer and is designed to provide acrylic acid-free overheads for recycle as the extraction solvent. A small aqueous phase in the overheads is mixed with the raffinate from the extraction step. This aqueous material is stripped before disposal both to recover extraction solvent values and minimize waste organic disposal loads.
The bottoms from the solvent-recovery column are fed to the foreruns column where acetic acid, some acrylic acid, water, and solvent are taken overhead. The overhead mixture is recycled to the extraction column. The bottoms from the foreruns column are then fed to the product column where the acrylic acid is taken overhead. The bottoms from the product column are stripped to recover values and the high boilers are burned. The principal losses of acrylic acid in this operation are due to dimerization of acrylic acid to 3-acryloxypropinic acid. Mild conditions and short residence times are maintained and polymerization inhibitors fed throughout the separations section to minimize polymer and dimer formation. The glacial acrylic acid produced in this stage of the process typically is at least 98-99% pure. Recovery of acrylic acid is about 95%.
Esterification. The process flow sheet (Fig. 4) outlines the process and equipment of the esterification step in the manufacture of the lower acrylic esters (methyl, ethyl, or butyl). The part of the flow sheet containing the dotted lines is appropriate only for butyl acrylate since the lower alcohols, methanol and ethanol, are removed in the wash column. Since the butanol is not removed by a water or dilute wash it is removed in the azeotrope column as the butyl acrylate azeotrope; this material is recycled to the reactor.
Acrylic acid, alcohol, and the catalyst, eg, sulfuric acid, together with the recycle streams are fed to the glass-lined ester reactor fitted with an external reboiler and a distillation column. Acrylate, excess alcohol, and water of esterification are taken overhead from the distillation column. The process is operated to give only traces of acrylic acid in the distillate. The bulk of the organic distillate is sent to the wash column for removal of alcohol and acrylic acid; a portion is returned to the top of the distillation column. If required, some base may be added during the washing operation to remove traces of acrylic acid.
A bleed is continuously taken from the reactor to remove high boilers. Values contained are recovered in the bleed stripper and the distillate from this operation is recycled to the esterification reactor. The bleed stripper stripper residue is a mixture of high boiling organic material and sulfuric acid, which is recovered for recycle in a waste sulfuric acid plant cannot be justified, the mixture may be discarded at sea or in a deep well, or neutralized and then treated biologically. Most acrylate plants employ a sulfuric acid regeneration or ammonium sulfate unit as a satellite plant.
The wet ester is distilled in the dehydration column using high reflux to remove a water-phase overhead. The dried bottoms are distilled in the product column to provide high purity acrylate. The bottoms from the product column are stripped to recover values and the final residue incinerated. Alternatively, the bottoms may be recycled to the ester reactor or to the bleed stripper.
Conventional polymerization inhibitors are fed to overhead areas of each of the distillation columns. The columns are operated under reduced pressure to give low bottom-temperatures and minimize polymerization.
The aqueous layer from the ester column distillate, the raffinate from washing the ester, and the aqueous phase from the dehydration step are combined and distilled in the alcohol stripper. The wet alcohol distillate containing a low level of acrylate is recycled to the esterification reactor. The aqueous column bottoms are incinerated, sent to biological treatment, or discharged by burial, etc. Biological treatment is common.
Process condition for methyl acrylate is similar to those employed for ethyl acrylate. However, in the preparation of butyl the excess butanol is removed as the butanol-butyl acrylate azeotrope in the azeotrope column.
The esters are produced in minimum purity of at least 98.5-99%. The yield, based on acrylic acid, is in the range of 90-95% depending on the ester and reaction conditions. Monomethyl ether of hydroquinone (10-100 ppm) is added as polymerization inhibitor and the esters are used in this form in most industrial polymerizations.
Acetylene-Based Routes. Walter Reppe the father of modern acetylene chemistry discovered the reaction of nickel carbonyl with acetylene and water or alcohols to give acrylic acid or esters. This discovery led to several processes which are in commercial use.
The original Reppe reaction requires a stoichiometric ration of nickel carbonyl to acetylene. The Rohm and Haas modified or semicatalytic process provides 60-80% of the carbon monoxide from a separate carbon monoxide feed and the remainder from nickel carbonyl. The reactions for the synthesis of ethyl acrylate are as follows:
4C2H2+4C2H5OH+Ni (CO)4+2HCI®4CH2=CHCO2C2H5+NiCL2
C2H2+C2H5OH+0.05 Ni (CO)4+0.8CO+0.1 HCI®CH2=CHCO2C2H5+0.05 NiCI2+0.05H2
The stoichiometric and the catalytic reactions occur simultaneously but the catalytic predominates. The process is started with stoichiometric amounts, but afterward, carbon monoxide, acetylene, and excess alcohol give most of the acrylate ester by the catalytic reaction. The nickel chloride is recovered and recycled to the nickel carbonyl synthesis step. The main by-product is ethyl propionate which is difficult to separate from ethyl acrylate. However, by proper control of the feeds and reaction conditions, it is possible to keep the ethyl propionate content below 1%. Even so, this is significantly higher than the propionate of the esters from the propylene oxidation route.
Other by-products formed are relatively easy to separate, including esters of higher unsaturated monobasic acid (alkyl 3-pentenoate and 3,5-heptadienoate) and esters of multiply unsaturated dibasic acids, eg, suberoates.
The reaction is initiated with nickel carbonyl. The feeds are adjusted to give to the bulk of the carbonyl from carbon monoxide. The reaction takes place continuously in an agitated reactor with a liquid recirculation loop. The reaction is run at about atmospheric pressure and at about 400C with an acetylene-carbon monoxide mole ratio of 1.1:1 in the presence of 20% excess alcohol. The reactor effluent is washed with nickel chloride brine to remove excess alcohol and nickel salts and the brine-alcohol mixture is stripped to recover alcohol for recycle. The stripped brine is again used as extractant but with a bleed stream returned to the nickel carbonyl conversion unit. The neutralized crude monomer is purified by a series of continuous, low-pressure distillations.
The modified Reppe process was installed by Rohm and Haas at their Houston plant in 1948 and expanded to the present capacity of about 200 kt/yr. Since Rohm and Haas started up a propylene oxidation plant at the Houston site in late 1976, it is not likely that their acetylene process will be used in a new facility.
Reppe's work also resulted in the high pressure, catalytic route which was used by BASF at Ludwigshafen in 1956. In this process, acetylene, carbon monoxide, water, and a nickel catalyst react at about 200°C and 13.9 MPa (2016 psi) to give acrylic acid. Safety problems caused by handing of acetylene are alleviated by the use of tetrahydrofuran as an inert solvent. In this process, the catalyst is a mixture of nickel bromide with a cupric bromide promotor. The liquid reactor effluent is degassed and extracted. The acrylic acid is obtained by distillation of the extract and subsequently esterified to the desired acrylic ester. The BASF process give acrylic acid, whereas the Rohm and Haas process provides the esters directly.
The BASF plant has a capacity of about 200 kt/yr. However, BASF has recently started up a plant based on propylene oxidation and the acetylene plant will probably be phased out. A smaller acetylene-based plant (about 20 kt/yr) is operated jointly by Dow and BASF (The Dow Badische Chemical Co.) in the United States.
Nickel carbonyl creates a major safety and pollution control problem, since it is volatile, has little odor, and is extremely toxic. Symptoms of dangerous exposure may not appear for several days. Effective medical treatment should be started immediately. The plant should be designed to ensure containment of nickel carbonyl and to prevent operator contact. Buildings should be operated under negative pressure with air exhaust to a decontamination furnace. A sensitive air-monitoring system should continuously sample the air and be connected to alarm and automatic shutdown controls. All personnel should be monitored for exposure to nickel carbonyl by periodic urine analysis.
All other organic waste-process and vent streams are burned in a flare, in an incinerator, or in a furnace where fuel value is recovered. Wastewater streams are handled in the plant biological treatment are.
More than one-third of the 1977 worldwide manufacturing capacity for acrylic acid and esters is based on the acetylene process. However, the raw material supply and cost trends discussed above indicate that this process is being phased out in favor of propylene-based plants.
Acrylonitrile Route. This process, based on the hydrolysis of acrylonitrile is also a propylene route since acrylonitrile is produced by the catalytic, vapor-phase ammoxidation of propylene.
CH3CH==CH2+NH3 +3/2O2 ® CH2==CHCN + 3H2O
The yield of acrylonitrile based on propylene is similar to the yield of acrylic acid based on the direct oxidation of propylene. Hence, for the large volume manufacture of acrylates, the acrylonitrile route is not attractive since additional processing steps are involved and the ultimate yield of acrylate based on propylene is much lower. Hydrolysis of acrylonitrile can be controlled to provided acrylamide rather than acrylic acid, but acrylic acid is a by-product is such a process. The minimum annual capacity to justify the investment of a propylene oxidation plant is about 23 kt.
The sulfuric acid hydrolysis may be performed as a batch or continuous operation. Acrylonitrile is converted to acrylamide sulfate by treatment with a small excess of 85% sulfuric acid at 80-100°C. A hold time of about one hour provides complete conversion of the acrylonitrile. The reaction mixture may be hydrolyzed and the extracted aqueous acrylic acid distilled prior to esterification or, after reaction with excess alcohol, a mixture of acrylic ester and alcohol is distilled and excess alcohol is recovered by aqueous extractive distillation. The ester in both cases is purified by distillation. Important side reactions are the formation of ether and addition of alcohol to the acrylate to give 3-alkoxypropionates.
In addition to high raw material costs, this route is unattractive because of large amounts of sulfuric acid-ammonium sulfate wastes, which can be treated in a waste acid plant to provide sulfuric acid for recycling. The investment for the waste acid plant is relatively high compared with the cost of the rest of the process. Alternatively, the waste stream may be converted to ammonium sulfate for use as fertilizer.
Ketene Process. The ketene process based on acetic acid or acetone as the raw material was developed by B.F. Goodrich and Celanese. It is no longer used commercially becuase the intermediate b-propiolactone is suspected to be a carcinogen. In addition, it cannot compete with the improved propylene oxidation process.
The process utilizes the high temperature pyrolysis of either acetic acid or acetone to ketene, which reacts with anhydrous monomeric formaldehyde at about 25°C in the presence of a catalyst, such as aluminum chloride, to give b-propiolactone. The lactone is converted to acrylic acid or to the desired ester by acidic hydrolysis or alcoholysis.
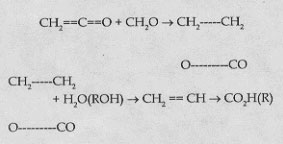
In the propylene oxidation process, propylene is converted directly to acrylic acid. In the ketene process, propylene is converted to acetone (via isopropanol or cumene), which is then subjected to the reactions described above. Alternatively, methanol from synthesis gas is carbonylated to acetic acid, which furnishes ketene for the ketene acrylic process. The propylene oxidation route which provides acrylic acid in a single operation is technically and economically superior.
Ethylene Cyanohydrin Process. The process, the first for the manufacture of acrylic acid and ester has been replaced by more economical ones. During World War I, the need for ethylene as an important raw material for the synthesis of aliphatic chemicals led to development of this process in both Germany, in 1927, and the United States, in 1931.
In the early versions, ethylene cyanohydrin was obtained from ethylene chlorohydrin and sodium cyanide. In later versions, ethylene oxide (from the direct catalytic oxidation of ethylene) reacted with hydrogen cyanide in the presence of a base catalyst to give ethylene cyanohydrin. This was hydrolyzed and converted to acrylic acid and by-product ammonium acid sulfate by treatment with about 85% sulfuric acid.
Losses by polymer formation kept the yield of acrylic acid to 60-70%. Preferably, esters were prepared directly by a simultaneous dehydration-esterification process.
The process has historic interest. It was replaced at Rohm and Haas Company by the acetylene-based process in 1954, and in 1970 at Union Carbide by the propylene oxidation process.
Acrylonitrile was also first manufactured from ethylene cyanohydrin, but now the optimum processes for both acrylates and acrylonitrile are based on propylene. Although the ethylene cyanohydrin route uses relatively low-cost raw material, it involves a number of steps and forms a large sulfuric acid-ammonium sulfate waste stream. Based on manufacturing costs and plant investment, this route is significantly inferior to the propylene-based oxidation process.
HOCH2CH2Cl + NaCN ® HOCH2CH2CN + NaCl
CH2-----CH2 + HCN ® HOCH2CH2CN
HOCH2CH2CH + H2O + H2SO4 ® CH2 == CHCO2H + NH4+HSO4-
Other Syntheses. Acrylic acid and other unsaturated compounds can also be made by a number of classical elimination reactions. Acrylates were obtained from the thermal dehydration of hydrochloric acid from the dehydrochlorination of 3-halopropionic acid derivatives and from the reduction of dihalopropionates. These studies, together with the related characterization and chemical investigations, contributed significantly to the development of commercial organic chemistry. Other synthetic procedures are reviewed below.
Vapor-Phase Condensations of Acetic Acid or Esters with Formaldehyde. Addition of a methylol group to the a-carbon of acetic acid or esters followed by dehydration gives the acrylates.
CH3CO2H(R) + CH2O ® CH2 == CHCO2H(R) + H2O
The reaction is generally carried out at atmospheric pressure and at 350-400°C. A variety of catalysts, eg. bases and metal salts and oxides on silica or alumina-silicates, have been patented. Conversions are in the 30-70% range, and selectivities in the 60-90% range, depending on the catalyst and the ratio of formaldehyde to acetate.
The procedure is technically feasible but high recovery of unconverted raw materials is required for the route to be practical. Its development depends on the improvement of catalysts and separation methods and on the availability of low cost acetic acid and formaldehyde. Both raw materials are dependent on ample supply of low-cost methanol, which may also be a factor in future energy strategy.
Oxidative Carbonylation of Ethylene. Spectacular progress in the 1970s has led to the rapid development of organotransition metal chemistry, particularly to catalyze olefin reactions. A number of patents have been issued for the oxidative carbonylation of ethylene to provide acrylic acid and esters. The procedure is based on the palladium-catalyzed carbonylation of ethylene in the liquid phase at temperatures of 50-200°C. Esters are formed when alcohols are included. Anhydrous conditions are desirable to minimize the formation of by-products including acetaldehyde and carbon dioxide. The presence of anhydrides and molecular sieves are claimed to improve the selectivity of the reaction.
During the reaction, the palladium catalyst is reduced. It is reoxidized by a cocatalyst system such as cupric chloride and oxygen. The products are acrylic acid in a carboxylic acid-anhydride mixture or acrylic esters in an alcoholic solvent. Reaction products also include significant amounts of 3-acryloxypropionic acid and alkyl 3-alkoxypropionates, which can be converted thermally to the corresponding acrylates. The overall reaction may be represented by:
CH2==CH2 + CO + HOR + ½O2 ® CH2 == CHCO2R + H2O
For the development of a commercial process, reaction selectivity must be improved by maintaining an anhydrous environment. High yields based on ethylene are required for the route to be competitive with propylene oxidation, since long-range projections show propylene costs to be significantly lower than those for ethylene.
Dehydrogenation of Propionates. Dehydrogenation of propionates to acrylates employing vapor-phase reactions at high temperatures (400-700°C) and short contact times over a variety of catalysts is claimed in the patent literature. Air is generally used in the gaseous reactant mixture. Iodine has been claimed to improve conversion and selectivity. This route is not expected to be of commercial interest because of low selectivity, purification difficulties, and high raw material costs.
Dehydrochlorination of b-Chloropropionic Acid and Esters. This historical route for the preparation of acrylic acid and esters is based on vapor-phase reactions of b-chloropropionates using metal sulfate or phosphate catalysts at 200-600°C. Both conversions and yields vary widely in the patent claims. Yields are claimed to be above 95% in the dehydrochlorination of ethyl b-chloropropionate. This route is not expected to become commercially useful because of raw material costs and technical problems.
Elimination of Alcohol from b-Alkoxypropionates. Acrylic esters have been prepared in high conversions and yields by passing the alkbyl b-alkoxypropionate at 200-400oC over metal phosphates, silicates, or metal oxides catalysts. Excellent results, greater than 90% yields, are also reported for liquid-phase reactions in the presence of sulfuric or phosphoric acid at 125-150oC. However, unless the intermediate b-alkoxy ester is readily available at low cost, eg, by oxidative carbonylation as above, this route will not be competitive with the propylene oxidation process.
Liquid-Phase Oxidation of Acrolein. As discussed before, the most attractive process for the manufacture of acrylates is based on the two-state, vapor-phase oxidation of propylene. The second stage involves the oxidation of acrolein. Considerable art on the liquid-phase oxidation of acrolein is available, but this route cannot compete with the vapor-phase technology.
Liquid-phase oxidation of acrolein has been studied under a variety of conditions eg, at low to moderate temperatures, in aqueous or solvent media, with silver, palladium, or organometallic catalysis, and with oxygen and peroxide oxidants. Conversions and yields range from 10-90%.
Decarboxylation of Maleic Acid. Decarboxylation of maleic to acrylic acid is carried out over a fixed-bed catalyst containing a silica, copper oxide and barium compound. Conversion of 62% and selectivity of 78% are claimed. This process has not been developed commercially because of high raw material cost and poor overall yields. Maleic acid was a significant by-product of the propylene oxidation route with some of the earlier catalysts, and it seemed that its decarboxylation might improve the overall yield of acrylic acid from propylene. However, the development of highly selective catalysts eliminated the need to consider such added operations.
Specialty Acrylic Esters
Higher alkyl acrylates and alkyl-functional esters are important in copolymer products, in conventions emulsion applications for coatings and adhesives and as reactants in radiation-cured coatings and inks. In general, they are produced in direct or transesterification batch processes because of their relatively low volume.
Direct, acid catalyzed esterification of acrylic acid is the main route for the manufacture of higher alkyl esters. The most important higher alkyl acrylate is 2- ethylhexyl acrylate prepared from the available oxo alcohol 2- ethyl-1-hexanol. The most common catalysts are sulfuric or toluenesulfonic acid and sulfonic acid-functional cation exchange resins. Solvents are used as entraining agents for the removal of water of reaction. The product is washed with base to remove unreacted acrylic acid and catalyst, and then purified by distillation. The esters are obtained in 80-90% yield and in excellent purity.
Transesterification of a lower acrylate ester and a higher alcohol can be performed using a variety of catalysts and conditions chosen to provide acceptable reaction rates and to minimize by-product formation and polymerization.
CH2==CHCO2R+R'OH catalyst CH2==CHCO2R'+ROH
Pure dry reactants are needed to prevent catalyst deactivation; effective inhibitor systems are also desirable as well as high reaction rates, since many of the specialty monomers are less stable than the lower alkyl acrylates. The alcohol-ester azeotrope should be removed rapidly from the reaction mixture and an efficient column used to minimize reactant loss to the distillate. After the reaction is completed, the catalyst may be removed and the mixture distilled to obtain the ester. The method is particularly useful for the preparation of functional monomers which cannot be prepared by direct esterification. Dialkylaminoethyl acrylic esters are readily prepared by transesterification of the corresponding dialkylaminoethanol. Catalysts include strong acids and tetraalkyl titanates for higher alkyl esters, and titanates, sodium phenoxides, magnesium alkoxides, and dialkyltin oxides for the preparation of functional esters. Because of loss of catalyst activity during the reaction, incremental or continuous additions may be required to maintain an adequate reaction rate.
Hydroxyethyl and 2-hydroxypropyl acrylates are prepared by the addition of ethylene oxide or propylene oxide to acrylic acid.
CH2==CHCO2H + CH2------CH2 ® CH2 ==CHCO2CH2CH2OH
The reactions are catalyzed by tertiary amines, quaternary ammonium salts, metal salts, and basic ion exchange resins. The products are difficult to purify and generally contain low levels of acrylic acid and some diester which should be kept to a minimum since its presence leads to product instability and to polymer crosslinking.
Analytical Methods
Chemical assay is preferably performed by gas-liquid chromatography (GLC) or by the conventional methods for determination of unsaturation such as bromination or addition of mercaptan, sodium bisulfite, morpholine, or mercuric acetate.
Acidity is determined by GLC or titration, and the dimer content of acrylic acid by GLC or a saponification procedure. The total acidity is corrected for the dimer acid content to give the value for acrylic acid.
Acrylic acid and esters are stabilized with minimum amounts of inhibitors consistent with stability and safety. The acrylic monomers must be stable and there should be no polymer formation for prolonged periods with normal storage and shipping. The monomethyl ether of hydroquinone (MEHQ) is frequently used as inhibitor and low inhibitor grades of the acrylate monomers are available for bulk handing. MEHQ levels of 10-15 ppm are generally adequate for the esters but a higher level (200 ppm) is needed for acrylic acid.
The effectiveness of phenolic inhibitors is dependent on the presence of oxygen and the monomers must be stored under air rather than an inert atmosphere. Temperatures must be kept low to minimize formation of peroxides and other products. Moisture may cause rust-initiated polymerization.
Acrylic acid has a relatively high freezing point (13°C) and the inhibitor may not be distributed uniformly between phases when frozen acid is partially thawed. If the liquid phase is inadequately inhibited, It could polymerize and initiate violent polymerization of the entire contents. Provisions should be made to maintain the acid liquid. High temperatures should be avoided because of dimer formation. If freezing should occur, melting should take place at room temperature (25°C); material should not be withdrawn until the total is thawed and well mixed to provide good distribution of the inhibitor. No part of the mass should be subjected to elevated temperatures during the melting process.
Dimer formation, which is favored by increasing temperature, generally does not reduce the quality of acrylic acid for most applications. The term dimer includes higher oligomers formed by further addition reactions and present in low concentrations relative to the amount of dimer (3-acryloxypropionic acid). Glacial acrylic acid should be stored at 16-29°C to maintain high quality.
The acrylic esters may be stored in mild or stainless steel, or aluminum. However, acrylic acid is corrosive to many metals and can be stored only in glass, stainless steel, aluminum, or polyethylene-lined equipment.
For most applications, inhibitors do not have to be removed. The low-inhibitor grades of acrylic monomers are particularly suitable for the manufacture of polymers without pretreatment. Removal of inhibitor is best done by adsorption with ion exchange resins or other adsorbents. Phenolic inhibitors may be removed from esters with an alkaline brine wash, generally a solution containing 5% caustic and 20% salt. Vigorous agitation during washing should be avoided to prevent the formation of emulsions. The washed monomers may be used without drying in emulsion processes. Washed uninhibited monomers are less stable and should be used promptly and certainly within a few weeks. They should be stored under refrigeration but should not be permitted to freeze because of the danger of explosive polymerization during thawing (heat of polymerization, approximately 75 kj/Mol or 18 kcal/mol).
The relatively low flash points of some acrylates create a fire hazard. Also, the ease of polymerization must be borne in mind in all operations. The lower and upper explosive limits for methyl acrylate are 2.8 and 25-vol %, respectively. Corresponding limits for ethyl acrylate are 1.8 vol % and saturation, respectively. All possible sources of ignition of monomers must be eliminated.
Health and Safety Factors
The toxicity of common acrylic monomers ranges from moderate to slight; they can be handled safely be established practices. Toxicity data on acrylic acid and esters are given in Table 5.
Protection required for safe handling of acrylic acid and esters commonly includes use of impervious gloves, shoe soles, and clothing; splash-proof goggles; and good ventilation of the workplace.
Table 1. Physical Properties of Acrylic Acid Derivative
Property | Acrylic acid | Acrolein | Acrylic anhydride | Acryloyl Chloride | Acrylamide |
CAS Registry Number |
(79-10-7) |
(107-02-8) |
(2051-76-5) |
(814-68-6) |
(79-06-1) |
Melting point, °C |
13.5 |
-88 |
|
|
84.5 |
Boiling point,°C/kPaa |
141/101 |
52.5/101 |
38/0.27 |
75/101 |
125/16.6 |
Refractive index,(ND°C) |
1.4185(25) |
1.4017(20) |
1.4487(20) |
1.4337(20) |
Flash point, Clevel-and open cup,°C |
68 |
|
|
|
|
Density, g/ml (°C) |
1.045(25) |
0.838(20) |
1.113(20) |
1.122(30) |
° To convert kPa to atm divide by 101.3.
Table 2. Properties of Commercially Important Acrylate Estersa
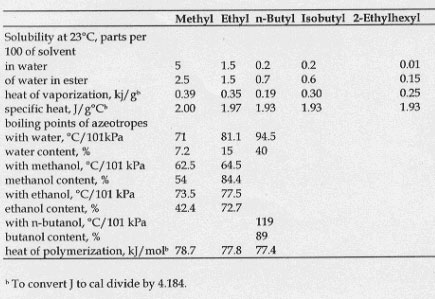
Table 3. Physical Properties of Acrylic Esters CH2==CHCOOR
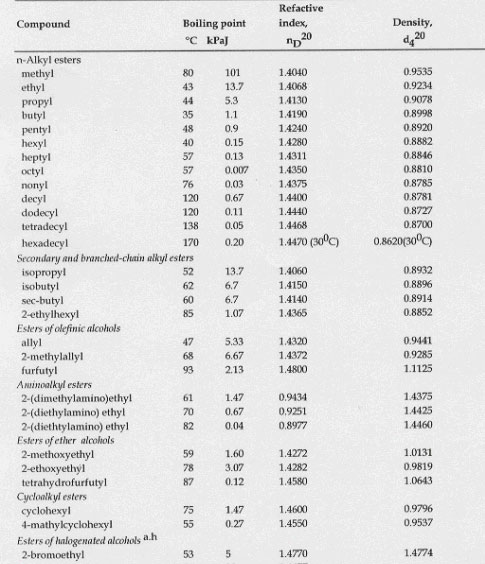
Table 4. Vapour Pressures of Acrylic Acid and Important Esters a,b
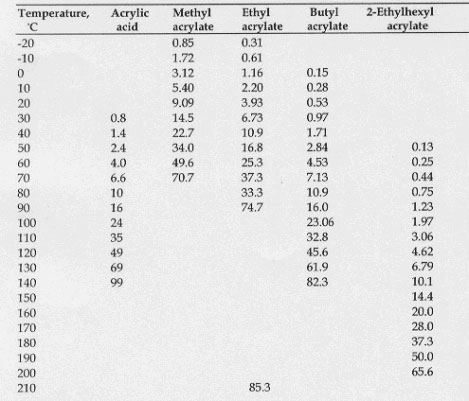