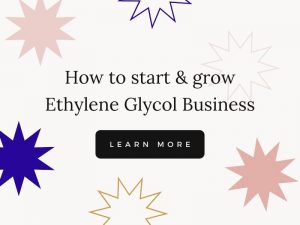
Ethylene glycol is a colourless, odourless, sweet-tasting, toxic organic compound used as a raw material in the production of many industrial chemicals such as antifreeze, polyester fibres, resins, and plasticizers. The global demand for ethylene glycol is expected to rise further in the coming years, owing to rising demand for automotive and construction materials, as well as increased consumption of PET bottles and containers.
Here are some important steps to take if you want to start an ethylene glycol manufacturing business.
Start a Business in Chemical Industry Projects, Click Here
Step 1: Conduct a Market Analysis
Before starting any business, it is critical to conduct extensive market research in order to assess demand and competition in the target market. In the case of ethylene glycol, you should investigate the product's global and regional markets, including the main buyers and suppliers, production and consumption trends, regulatory requirements, and pricing dynamics. You should also identify the market's key competitors, as well as their strengths and weaknesses and market share.
The Chemical Economics Handbook (CEH) published by IHS Market is a useful resource for market research because it provides comprehensive analysis and forecasts of the global ethylene glycol market, including supply and demand balances, production capacities, trade flows, and prices. To gather relevant market information, you should also consult industry reports, academic journals, trade associations, and government websites.
Read our Books Here: The Complete Technology Book on Chemical Industries
Step 2: Develop a Business Plan
Create a business plan that outlines the key aspects of your manufacturing company, such as the products, the manufacturing process, the location, the equipment, the raw materials, the workforce, the marketing strategy, financial projections, and risks and opportunities, based on your market research.
A detailed description of the ethylene glycol products you intend to manufacture, as well as their specifications, quality standards, and applications, should be included in your business plan. You should also describe the manufacturing process, which should include the feedstock, catalysts, reaction conditions, separation and purification steps, and waste management procedures.
Related Feasibility Study Reports: Ethylene Glycol Manufacturing Industry
The location of your manufacturing plant is also an important consideration that can affect your costs, logistics, and regulatory compliance. You should compare the availability and cost of utilities, transportation, labour, and other resources in various locations and select the one that provides the best balance of benefits and drawbacks.
The scale and technology of your manufacturing process will determine your equipment and raw material requirements. The most appropriate equipment, such as reactors, distillation columns, pumps, compressors, and storage tanks, should be chosen based on efficiency, dependability, safety, and cost. You should also identify raw material suppliers, such as ethylene oxide, water, and utilities, and negotiate favourable terms and prices with them.
Your workforce will be critical to the success of your manufacturing company, so you should hire and train skilled and motivated employees with knowledge and experience in chemical engineering, process safety, environmental management, and quality control.
Your marketing strategy should focus on the most profitable and long-term segments of the ethylene glycol market, such as automotive, construction, and packaging, while emphasizing your products' unique features and benefits, such as high purity, low impurities, and consistent supply. You should also build strong relationships with your customers, suppliers, and distributors, and use digital and social media to reach a larger audience.
Your financial projections should estimate your manufacturing company's revenues, costs, and profits over a number of years, based on realistic assumptions about market demand, production volumes, selling prices, operating expenses, and capital investments. You should also think about your financing options, such as bank loans, venture capital, and private equity, as well as the potential returns and risks associated with each.
Finally, you should identify and assess your manufacturing business's risks and opportunities, including technical, economic, environmental, legal, and social aspects. To mitigate the impact of any adverse events, you should create a risk management plan that includes contingency plans, insurance coverage, and emergency response procedures.
Step 3: Obtain Permits and Licenses
To run an ethylene glycol manufacturing company, you must obtain various permits and licences from regulatory agencies such as the Environmental Protection Agency (EPA), the Occupational Safety and Health Administration (OSHA), and the Department of Transportation (DOT).
Permits and licences are typically issued in the following areas:
Air Emissions: You must obtain an air permit that specifies the allowable emissions of pollutants such as volatile organic compounds (VOCs), nitrogen oxides (NOx), and sulphur dioxide from your manufacturing process (SO2). To meet regulatory limits, you may need to install and operate air pollution control devices such as scrubbers, filters, and catalytic converters.
Water Discharges: A wastewater discharge permit is required to regulate the quality and quantity of effluent discharged from your manufacturing process into local water bodies such as rivers, lakes, and oceans. To remove or reduce pollutants, you may need to install and operate wastewater treatment systems such as clarifiers, sedimentation basins, and biological reactors.
Hazardous Waste: You must obtain a hazardous waste generator permit to generate, store, transport, and dispose of hazardous waste generated by your manufacturing process, such as spent catalysts, contaminated solvents, and off-spec products. To manage hazardous waste, you must adhere to the regulations of the Resource Conservation and Recovery Act (RCRA) and the Hazardous Waste Manifest System (HWMS).
Safety: You must follow OSHA regulations that aim to protect your workers' health and safety, such as the Process Safety Management (PSM) standard, which requires you to develop and implement a comprehensive programme to prevent or mitigate hazards associated with your manufacturing process, such as fire, explosion, and toxic release. You must also train your employees on the proper handling, storage, and disposal of hazardous materials, as well as provide them with OSHA-compliant personal protective equipment (PPE).
Transportation: You must follow DOT regulations when transporting hazardous materials such as ethylene glycol by road, rail, or water. Hazardous materials must be properly classified, packaged, marked, labelled, and documented, and shipping regulations, such as the Hazardous Materials Regulations (HMR) and the International Maritime Dangerous Goods (IMDG) Code, must be followed.
Watch other Informative Videos: Ethylene Glycol Manufacturing Industry | Chemical Business Ideas for Aspiring Entrepreneurs
To obtain permits and licences, you must submit applications and supporting documents to the appropriate authorities, pay the fees, and submit to inspections and audits to ensure that you are in compliance with the regulations. You may also require the services of environmental consultants, lawyers, and other experts to help you navigate the complex regulatory landscape.
Step 4: Build and Test the Manufacturing Plant
After you have obtained the necessary permits and licences, you can begin building and commissioning your manufacturing plant. The following activities are carried out during the construction phase:
Preparation of the Site: Clear and grade the site, install utilities such as electricity, gas, and water, and build the foundations, walls, and roofs of the buildings that will house the equipment and personnel.
Installation of Equipment: You must install and align equipment such as reactors, distillation columns, pumps, compressors, and storage tanks in accordance with the engineering design and specifications. You must ensure that the equipment is in good working order.
Visit the page Select and Choose the Right Business Startup for You for sorting out the questions arising in your mind before starting any business and know which start-up you can plan.
We, at NPCS, endeavor to make business selection a simple and convenient step for any entrepreneur/startup. Our expert team, by capitalizing on its dexterity and decade's long experience in the field, has created a list of profitable ventures for entrepreneurs who wish to diversify or venture. The list so mentioned is updated regularly to give you a regular dose of new emerging opportunities.
Click here to send your queries/Contact Us
Reasons for Buying NIIR Report:
● Our research report helps you get a detailed picture of the industry by providing an overview of the industry along with the market structure and classification.
● Our report provides market analysis covering major growth driving factors for the industry, the latest market trends and the regulatory framework of the industry.
● Our Report provides an analysis and in-depth financial comparison of major Players / Competitors.
● Our Report provides indispensable buyers' data with their company financials as well as the contact details, which can be an important tool in identifying the target customers.
● Our report provides forecasts of key parameters which help to anticipate the industry performance.
● We use reliable sources of information and databases. And information from such sources is processed by us and included in the report.
See More Links:
· Start a Business in Asia
· Start a Business in Potential Countries for Doing Business
· Best Industry for Doing Business
· Business Ideas with Low, Medium & High Investment
· Looking for Most Demandable Business Ideas for Startups
· Startup Consulting Services
· Start a Business in Africa
· Start a Business in India
· Start a Business in Middle East
· Related Videos
· Related Books
· Related Projects
· Related Market Research Reports
𝐂𝐨𝐧𝐭𝐚𝐜𝐭 𝐮𝐬
NIIR PROJECT CONSULTANCY SERVICES, DELHI
An ISO 9001:2015 Company
ENTREPRENEUR INDIA
106-E, Kamla Nagar, Opp. Mall ST,
New Delhi-110007, India.
Email: npcs.ei@gmail.com
info@entrepreneurindia.co
Tel: +91-11-23843955, 23845654, 23845886
Mobile: +91-9097075054, 8800733955
Website: https://www.entrepreneurindia.co
https://www.niir.org