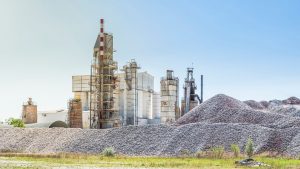
Introduction
One of the most significant building materials in the world is cement. It is an essential component in the manufacturing of mortar, concrete, and other building products. As urbanization and infrastructure development continue to rise, it is anticipated that cement demand will rise in the upcoming years. Starting a cement production company can be a lucrative endeavor, but it demands careful planning and execution. We'll talk about how to launch a cement production company in this article.
First, Do Market Research.
Market research is the initial stage in launching a cement production company. You must have a thorough awareness of the cement market in your area as well as the rivalry. Additionally, you should look into your region's legal requirements for establishing a cement manufacturing company.
Speaking with individuals in the construction sector is one of the finest ways to carry out market research. Governmental organizations, trade groups, and industrial associations are additional sources of information. In order to assess the potential for expansion and profitability, you need also research market trends and forecasts for the cement sector.
Visit this Page for More Information: Start a Business in Cement and Cement Based Products Industry
Step 2. Create a Business Plan
Making a company plan is the next stage after conducting market research. A business plan is a written document that summarizes your objectives, plans, and financial forecasts. Before beginning a cement manufacturing business, it is crucial to have a business plan because it will enable you to stay on course and make wise decisions.
The Following Sections Should Be Present In Your Business Plan:
Executive summary: In this area, you should give a general outline of your company's mission and aims.
Market Analysis: The findings of your market research, along with details on the local cement market's demand and the competition, should be included in this part.
Marketing Strategy: In this area, you should describe your marketing tactics, such as how you intend to advertise your items and connect with your target market.
Operations Plan: In this area, you should describe your production method, together with the tools and supplies you'll need, the location of your facility, and the number of employees you'll need.
Financial Plan: This part should contain your financial estimates, such as your anticipated launch expenses, future sales, and cash flow.
Step 3: Obtain Financing Starting a Cement Production Company
Demands a considerable amount of finance. To pay for your initial costs, which could include leasing or buying land, buying supplies and equipment, and hiring people, you will need to find finance.
Starting A Cement Production Company Can Be Financed In A Number Of Ways, Including:
Bank Loans: A bank or other financial institution will consider your application for a business loan. To be eligible for a loan, you must submit a thorough business plan and financial projections.
Investors: Investors such as venture capitalists or angel investors are another source of funding. You'll need to present your business concept to potential investors and persuade them that it has the potential for success.
Grants: You might be able to get cash from charitable organizations or governmental bodies that offer grants to small enterprises. You must learn about each grant program's qualifying conditions and application process.
Step 4: Obtain Licenses and Permits
Starting a cement production company entails securing the required government licenses and permits. You will need to look into the local regulations in your area and submit applications for the required permits and licenses.
Depending on the location of your company and the kind of manufacturing technique you want to use, several permits and licenses may be required. For the purposes of zoning, waste management, and the prevention of air and water pollution, permits may be required.
Read our Books Here: The Complete Book on Cement & Concrete Products Manufacturing
Step 5: Buy or Rent Land In Order To Build Your Manufacturing Facility
You will need to buy or rent land. Because it will affect your production costs and transportation costs, the location of your facility is a crucial factor.
Think About The Following Elements While Choosing A Site For Your Manufacturing Facility:
Accessibility: Select a place that is
Maintain your accessibility for the movement of raw materials and completed goods.
Infrastructure: Verify whether the area has adequate infrastructure, including communication networks, a reliable supply of water, and energy.
Make sure the area is zoned for industrial use and complies with all applicable local ordinances.
Labor Availability: Find out if the local labor market has an adequate supply of both skilled and unskilled workers.
Costs: Calculate the costs of buying or renting land in various places.
Step 6: Purchase Materials and Equipment
The next stage is to stock your manufacturing facility with the necessary tools and supplies. Cement kilns, crushers, and grinding mills may be among the tools you require. To make cement, you will also need ingredients like gypsum, clay, and limestone.
Consider the following elements while choosing tools and supplies:
Quality: Pick products that fulfil industry requirements for both equipment and materials.
Price: To get the greatest offers, compare prices from many sources.
Availability: Make sure the tools and supplies are accessible when you need them.
Maintenance: Take into account the equipment and material costs as well as the necessary maintenance.
Step 7: Hire Staff to Run Your Cement Manufacturing Company
You will need to hire staff. The size of your manufacturing plant and the level of production will determine how many employees you require.
Take into account the following elements when employing staff:
Skills: Hire personnel that have the required education and work history in the cement sector.
Training: Offer your personnel programmes for learning and growth to help them become more skilled and knowledgeable.
Compensation and Benefits: To entice and keep great employees, provide competitive compensation and benefit plans.
Step 8.Create a Marketing Strategy
The following step is to create a marketing strategy after your manufacturing facility has been set up and production has begun. You must advertise your goods and connect with prospective buyers.
Your marketing plan might contain the following:
Advertising: To advertise your items, use a variety of media, including print publications, radio, and television.
Trade fairs: Take part in exhibits and trade fairs to display your items and build relationships with potential clients.
Related Business Plan: Cement Plant
Online Presence: Set up a website and social media profiles to spread the word about your items and reach a larger audience.
Building connections with industry experts and potential clients will help you become more visible and credible through networking.
Step 9: Evaluate and Boost Performance
Once your cement manufacturing company is operational, it is crucial to track and enhance performance. You can use this to pinpoint problem areas and streamline your production procedures.
Performance can be tracked and enhanced by:
Key performance indicators (KPIs) monitoring Determine and monitor KPIs like production volume, cost per tonne, and energy usage to gauge your performance and spot improvement opportunities.
Continuous Improvement: To find and fix inefficiencies in your manufacturing processes, put in place a continuous improvement programme.
Training and Development: Offer continuing training and development initiatives to improve your staff's abilities and understanding.
Starting a cement production company demands rigorous preparation and execution. You must carry out market research, create a business plan, enlist funding, gain permits and licenses, buy tools and supplies, hire personnel, design a marketing plan, and track and enhance performance. A cement manufacturing company can be a successful business that advances the development of the construction sector with the appropriate planning and execution.
1. Pay attention to quality: Cement is a crucial building material, and any quality compromise might have negative effects. As a result, quality must be given top priority throughout your whole manufacturing process.
2. Support sustainability: It is well known that the cement industry contributes significantly to greenhouse gas emissions. You may lessen your impact on the environment and improve your reputation by implementing sustainable practices in your manufacturing process.
3. Develop a strong working relationship with your suppliers. The calibre of your raw materials can have a big impact on the calibre of your finished goods. As a result, it's critical to build strong bonds with your suppliers and make sure they uphold your high standards for quality.
4. Establish a Safety Programme: The production of cement requires the use of large machinery and potentially dangerous materials. To protect your employees and guarantee adherence to safety requirements, it is crucial to create a safety programme.
Watch other Informative Videos: Cement Manufacturing Plant | Detailed Project Report | Profile | Business Plan
5. Keep up with Industry Trends: New technology and procedures are continually being introduced to the cement industry. Keeping up with market trends can help you keep one step ahead of the competition and spot chances for expansion and innovation.
Conclusion
Starting a cement manufacturing company can be difficult yet rewarding. It necessitates meticulous preparation, execution, constant evaluation, and improvement. You can launch a successful cement production company that satisfies the need for this essential building material and supports the expansion and development of the construction sector by following the instructions provided in this article and implementing the extra advice.
Visit the page Select and Choose the Right Business Startup for You for sorting out the questions arising in your mind before starting any business and know which start-up you can plan.
We, at NPCS, endeavor to make business selection a simple and convenient step for any entrepreneur/startup. Our expert team, by capitalizing on its dexterity and decade's long experience in the field, has created a list of profitable ventures for entrepreneurs who wish to diversify or venture. The list so mentioned is updated regularly to give you a regular dose of new emerging opportunities.
Click here to send your queries/Contact Us
Reasons for Buying NIIR Report:
● Our research report helps you get a detailed picture of the industry by providing an overview of the industry along with the market structure and classification.
● Our report provides market analysis covering major growth driving factors for the industry, the latest market trends and the regulatory framework of the industry.
● Our Report provides an analysis and in-depth financial comparison of major Players / Competitors.
● Our Report provides indispensable buyers' data with their company financials as well as the contact details, which can be an important tool in identifying the target customers.
● Our report provides forecasts of key parameters which help to anticipate the industry performance.
● We use reliable sources of information and databases. And information from such sources is processed by us and included in the report.
𝐂𝐨𝐧𝐭𝐚𝐜𝐭 𝐮𝐬
NIIR PROJECT CONSULTANCY SERVICES, DELHI
An ISO 9001:2015 Company
ENTREPRENEUR INDIA
106-E, Kamla Nagar, Opp. Mall ST,
New Delhi-110007, India.
Email: npcs.ei@gmail.com
info@entrepreneurindia.co
Tel: +91-11-23843955, 23845654, 23845886
Mobile: +91-9097075054, 8800733955
Website: https://www.entrepreneurindia.co
https://www.niir.org
OF_20Art23