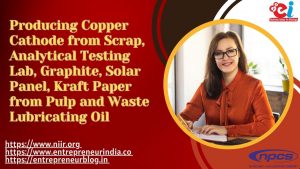
Starting a business is a transformative process that needs vision, tenacity, and careful planning. No matter if you're an established professional ready to take the plunge into entrepreneurship or an aspiring entrepreneur with a game-changing idea, starting a business is an exciting and challenging endeavor. The ability to shift course when necessary, a well-thought-out business plan, a thorough understanding of market dynamics, and a sound firm concept are all essential for success in an inventive and cutthroat market. This introduction explores the various aspects of starting a firm, from conception to implementation, and it places special emphasis on the essential components that underpin a fruitful entrepreneurial enterprise.
Business Plan of Copper Cathode from Copper Scrap
A technique of refining copper scrap results in copper cathode, a pure version of the metal. Copper cathode is 99.99% pure copper, unlike copper scrap, which may also contain alloys and impurities. It is commonly formed into rectangular plates and utilized as a raw material in a number of sectors, including manufacturing, electronics, and construction.
Visit this Page for more Information: Start a Business in Copper Industry
How to Process Copper Scrap for Cathode Production
Several procedures must be followed in the processing of copper scrap for cathode manufacture. The copper scrap should first be gathered and sorted according to purity. It's crucial to isolate the debris from any alloys or contaminants. After being sorted, the scrap must be melted in a furnace to get rid of impurities and extra materials.
Related Business Plan: A Business Plan Copper Cathode from Copper Scrap
The molten copper is cast into molds after melting to create anodes. Then, these anodes are put in an electrolytic cell with an electric current running through them. The name of this procedure is electrorefining.
Watch Video: Producing Copper Cathode from Scrap, Analytical Testing Lab, Graphite, Solar Panel and Waste Lubricating Oil Recycling Plant
Copper ions move from the anode to the cathode, which is a thin sheet of pure copper, during electrorefining. The resulting cathode is taken out of the electrolytic cell, cleaned, and made ready for use after the copper ions have moved. The cathode is 99.99% pure copper thanks to this procedure, making it extremely useful across numerous industries.
Read Similar Article: Copper Cathode Production from Copper Scrap
Maximizing Your Profit from Copper Scrap with Cathode Production
The production of cathodes from copper scrap can increase your profit, but it requires careful planning and effective procedures. By maximizing the sorting and gathering of copper scrap, one can raise profitability. You may make sure that only premium materials are used to create copper cathode by carefully separating the scrap depending on purity levels.
Read our Books Here
The effectiveness of the refining process is another crucial element in optimizing profit. Businesses can reduce energy use and increase pure copper yield by adopting cutting-edge technologies and methods. This lowers costs and raises the cathode's value at the same time.
Related Feasibility Study Report: Copper Cathode from Copper Scrap
Global Market Outlook
The market for copper cathodes was valued at over USD 22.5 billion in 2021 and increased at a CAGR of roughly 5.6% from 2022 to 2030. By 2030, the market is expected to be worth about USD 36.8 billion. Cable and wire industries provide the raw materials for copper cathode production.
Watch other Informative Video: Copper Cathode Production from Copper Scrap
Copper has demonstrated to be particularly advantageous in the production of brass, copper tubes, and copper sheet products in addition to being present in more than 450 alloys. It serves as the primary raw material for producing copper rods, which are used in a variety of industries. Pure copper has excellent electrical conductivity.
Setup Analytical Testing Laboratory (Food, Water, Soil and Pharma)
Facilities that specialize in evaluating the safety and quality of various materials include analytical testing labs. They are staffed with highly skilled specialists who conduct tests with accuracy and precision, and they are furnished with cutting-edge equipment.
Visit this Page for more Information: Best Industry for Doing Business
These laboratories are essential to sectors like food, water, soil, and pharmaceuticals because they make sure that materials and products adhere to safety requirements before they are distributed to customers.
Related Business Plan: Setup Plant of Analytical Testing Lab (Food, Water, Soil and Pharma)
Importance of Accurate Test Results for Each Industry
Every sector that uses analytical testing labs places a premium on accurate test findings. For instance, precise results in the food business aid in the detection of potential pollutants like bacteria, chemicals, or allergens.
Read Similar Articles: STARTUP BUSINESS
This guarantees that the food we eat is secure and devoid of any dangerous elements. Consumers would be in danger of consuming contaminated food, which could result in major health problems, without precise test findings.
Why Should Entrepreneur Start an Analytical Testing Lab?
Ø Growing Demand: Numerous sectors, including the food, water, soil, and pharmaceutical industries, are experiencing an ongoing rise in demand for analytical testing services. Companies are looking for trustworthy testing labs to make sure their products meet regulatory requirements and customer expectations as emphasis on safety and quality increases.
Related Feasibility Study Report: Start You Own Analytical Testing Lab (food, Water, Soil and Pharma)
Ø Lucrative Market: The analytical testing sector has a market with Significant Growth Potential. Companies are eager to spend in dependable testing services to safeguard their brand and satisfy industry standards as worries about contamination and safety continue to escalate.
Download Pdf: Producing Copper Cathode from Scrap, Analytical Testing Lab, Graphite, Solar Panel and Waste Lubricating Oil Recycling Plant
Global Market Outlook
By 2029, at a CAGR of 14.7%, the market for analytical laboratory services worldwide is anticipated to reach USD 15,746.14 million. The global market for analytical laboratory services is expanding as a result of quickly rising needs, increased industrialisation, consumer awareness, expanding industries, and technological advancements.
Watch other Informative Video: Startup Business Plans
In this industry, revenue and sales have grown exponentially. Due to the factors fueling the market's expansion over the projected period, both the market's size and growth are anticipated to rise.
Start Production of Expandable & High Purity Graphite
A type of graphite that has undergone chemical treatment to create a very porous structure is known as expandable graphite. Due to its porosity, the material can expand in the presence of heat, making it perfect for uses as thermal insulators and fire retardants.
Visit this Page for more Information: Start a Business in Mineral Processing Industry
High Purity Graphite, on the other hand, is graphite that has gone through a number of purification steps to remove impurities, producing a substance with a carbon content of above 99.9%.
Production of Expandable and High Purity Graphite
To ensure that the material satisfies the necessary criteria, numerous crucial stages are taken during the production of Expandable and High Purity Graphite. It starts with obtaining premium natural graphite, which is subsequently put through a purification procedure to get rid of impurities and raise the carbon content. The graphite is further processed to produce expandability after being purified.
Related Business Plan: Start Production of Expandable & High Purity Graphite
This is accomplished using a procedure known as chemical intercalation, in which graphite is treated with various chemicals to produce a structure that is highly porous. Due to its porosity, the material can expand in the presence of heat, making it appropriate for uses as thermal insulators and fire retardants. The substance is put through additional purification processes, like acid washes and heat treatments, to produce high purity graphite. These procedures aid in the removal of any impurities that may still be present, producing a material with a carbon content of above 99.9%. For industries that demand great thermal and electrical conductivity, this high purity is essential.
Read Similar Articles: HIGH PURITY GRAPHITE
Applications and Uses
Expandable Graphite
Graphite that has undergone a treatment—typically an acid treatment—that makes it expand when heated is known as expandable graphite. It is employed in numerous applications and has an exponential growth rate.
Ø Flame Retardants: Expandable graphite creates a protective layer when heated, acting as a flame retardant by expanding and slowing the spread of flames. Because of this, it is utilized as a flame retardant in plastics, foams, and building supplies.
Read our Book Here: The Complete Technology Book on Minerals & Mineral Processing
Ø Gasket Materials: It is utilized to create flexible graphite sheets that are employed as gaskets in high-temperature applications because of its capacity to expand.
High Purity Graphite
Ø Semiconductor Manufacturing: In the process of creating silicon crystals for semiconductors, electrodes are employed.
Ø Nuclear Reactors: In nuclear reactors, high purity graphite serves as a moderator, slowing the neutrons and permitting the nuclear reactions to take place.
Related Feasibility Study Report: Setup Plant Of Expandable & High Purity Graphite
Global Market Outlook
By 2029, the Expanded Graphite Market is anticipated to reach US$ 509.42 Mn, growing at a CAGR of 7.6% over the projected period. The building and construction sector's stricter fire safety regulations, rising consumer electronics demand, and need for non-halogenated flame retardants are the main factors driving this market.
Watch other Informative Video: Manufacturing of Graphite Crucible | Business Ideas and Opportunities in Graphite Crucible
Starting a Solar Panel Production Business
The foundation of renewable energy is solar energy. They are gadgets that use the photovoltaic effect to transform sunshine into power. Solar panels, which are constructed of many silicon solar cells, harness the energy of the sun and transform it into useable energy.
Visit this Page for more Information: Start a Business in Renewable Energy Industry
Layers of semiconducting material, often silicon, placed between a front cover, back cover, and encapsulant material make up the basic structure of a solar panel. When sunlight strikes solar cells, it generates an electric field that permits electrons to flow around freely inside the cells. Direct current (DC) electricity is produced by this movement of electrons. Solar energy systems, whether they are used to household, commercial, or utility-scale uses, must include solar panels.
Related Business Plan: Solar Panel
Production Process
In business production procedure is essential because it affects the caliber and effectiveness of your solar panels. The procurement of required materials is the first stage of the production process. This contains the front cover, back cover, and encapsulant material in addition to the semiconducting material, which is often silicon. Make sure the materials you select are high-quality and adhere to industry requirements.
Read Similar Article: How to Start Manufacturing Business of Solar Panels
The actual production of the solar panels is the following phase. To do this, silicon wafers are divided into solar cells, which are then put together into a panel and linked together in series to produce power. Every step of the production process must include quality control to guarantee that the panels meet performance and safety requirements. The panels are tested once they are made to make sure they produce the desired amount of electricity and operate efficiently. This entails taking measurements of the voltage and current output and testing the device's functionality in various lighting scenarios. You can make sure that your solar panels are dependable, effective, and long-lasting by following a clearly defined production process and upholding high quality standards.
Read our Books Here: Solar Products, Renewable Energy, Solar PV Power, Solar Energy, Solar Lighting, Solar Power Plant, Solar Panel, Solar Pump, Solar Photovoltaic Cell, Solar Inverter, Solar Thermal Power Plant, Solar Farm And Solar Cell Modules
Market Analysis
The market for solar panels is anticipated to increase from USD 131.37 billion in 2022 to USD 282.4 billion in 2030, with a CAGR of 12.63%. Throughout the predicted period (2022– 2030). In 2021, the market size for solar panels was estimated to be USD 84.35 billion.
Related Feasibility Study Report: Solar Panel- Manufacturing Plant, Detailed Project Report, Profile, Business Plan, Industry Trends, Market Research, Survey, Manufacturing Process, Machinery, Raw Materials, Feasibility Study, Investment Opportunities, Cost And Revenue, Plant Economics
The major principal market drivers for expansion are rising environmental pollution, declining prices for components like silver and polysilicon, and incentives and tax breaks provided by governments throughout the world for the installation of PV panels.
Watch other Informative Video: Solar Panel - Manufacturing Plant, Detailed Project Report
Start Waste Lubricating Oil Recycling Plant
Waste lubricating oil recycling plants are specialized establishments made to handle old oil and turn it into high-quality lubricants and base oils.
Visit this Page for more Information: Start a Business in Petroleum Industry
The spent oil is collected, cleaned, and re-refined at these facilities using cutting-edge technology to make sure it complies with industry requirements and can be safely recycled.
Read our Book Here: Lubricating Oils, Greases and Petroleum Products Manufacturing Handbook
Economic Benefits of Recycling Lubricating Oil
Recycling lubricating oil not only has significant environmental benefits, but it also provides a range of economic advantages. One of the key economic benefits is the reduction in costs for industries that rely on lubricating oil. By re-refining and reusing used oil, companies can save on the expenses associated with purchasing new oil. This can have a positive impact on their bottom line and help them remain competitive in the market.
Related Business Plan: Start Waste Lubricating Oil Recycling Plant
Uses and Application of Recycling Lubricating Oil
ü Bitumen-Based Products: Bitumen can be combined with used lubricating oil to create roofing materials, waterproofing products, and road surfaces.
ü Additive in Manufactured Products: Recycled oil is used as an additive in the manufacture of several commodities, including rubber and plastic products.
Read Similar Article: Set up Waste Lubricating Oil Recycling Plant | Profitable Business Opportunity
ü Marine Oils: The recycled lubricating oil can be used in maritime applications, such as ship engines, after extensive processing and blending with the proper additives.
Related Feasibility Study Report: Opportunities In Waste Lubricating Oil Recycling Plant
Global Market Outlook
According to estimates, the Waste Oil Recycling Market would increase from USD 63.44 billion in 2022 to USD 95.4 billion in 2029, growing at a 5.30 percent CAGR. The waste oil recycling technique enables the recycling and reuse of spent motor oil.
Watch other Informative Video: Waste Lubricating Oil Recycling Plant Business Plan
Click here to send your queries/Contact Us
As a result, the cost of the raw materials required to create the oil from scratch might be reduced for the producers. Over the course of the forecast period, raw material prices are anticipated to decrease, fostering the expansion of the waste oil recycling market.
See More Links:
· Start a Business in Asia
· Start a Business in Potential Countries for Doing Business
· Best Industry for Doing Business
· Business Ideas with Low, Medium & High Investment
· Looking for Most Demandable Business Ideas for Startups
· Startup Consulting Services
· Start a Business in Africa
· Start a Business in India
· Start a Business in Middle East
· Related Videos
· Related Books
· Related Projects
· Related Market Research Reports
· Read Our Blog Here